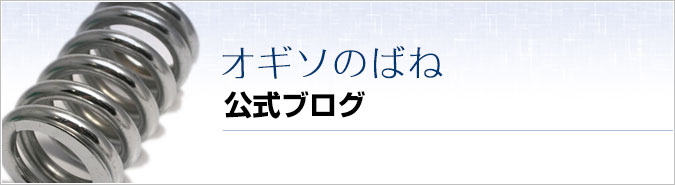
進化はしないが、変化はできる。できる男になってやる。
好きな女(ひと)
2015.11.22
カテゴリ : 日記
最近のTVを見ていて、私が気になる女性は何人かいる。
例えば、土屋太鳳(つちやたお)だったり、波瑠(はる)だったり。
ん? NHK率が高いのは歳をとってきたせいか?
でも、今の一番は、
松岡 茉優(まつおか まゆ)でしょ!社長!!
で、今出てるドラマも楽しみの一つでもあるのですが。
ウチのカミさん、娘いわく
「出たがり感がすごい」「うるさい」
「ちょっとないわ~」
だと。
まあ、男と女の好みは違うわな。(あと、ひがみもあるのでしょうが)
そんな折、TVを見ていたカミさんが、
「ほら、ほら、早く!あなたの好きな女(ひと)が出てるよ!」
と、別の部屋にいた私をわざわざ呼ぶので、(大きい声で)
『え?マジで!』
少し喰い気味に勢い込んでTVに駆け寄ると、そこには!
♪ まも~りたい、あいするかぞ~くを~~ ♪
ふざけんなよ!吉田じゃねーかっ!!
よりにもよって。おい!
誰が、霊長類最強女子なんかっ!
なんか前より可愛くなってるけども。
「だって、あなた強い女(ひと)が好きだって言ってたじゃない」(大笑い)
そんなこと言ったことあるか?
(でも、でも。よく考えたら確かに身近に史上最強の女(ひと)がいる!もうこれ以上は勘弁して下さい。心の声)
「 ♪ いち、に、さん、し、アルソック!・・・」
アイディアで変わる!日本の収穫
2015.11.04
カテゴリ : 仕事/ビジネス/study
2015年11月3日(火)放送のNHKニュース、
おはよう日本のまちかど情報室で、またもや
『野菜・園芸用 ワンタッチ支え止め具』が紹介されました!
>
アイディアで変わる!日本の収穫。
植物が大きくなると支えが必要です。
支柱に植物を留めるのにひもを結ぶのが大変です。そこで、ステンレスのフック。
弾力性があるステンレスでできていて引っかけるだけで簡単です。
>
さすが。NHKさん太っ腹!
ありがとうございます。
言葉にできない
2015.11.01
カテゴリ : こども/カミさん/ファミリー
ある日の話。
「あ、今日はあの店ポイント5倍だ。行ってくるか」(私)
『じゃあ、ついでに頼みたいものがあるの』(カミさん)
「何?どんなもの」
『う~ん。。。。。。。言葉にならない』
「お前は小田和正か!」
ラ、ラ、ラ、ララ、ラ~ ♪
たくさんあったみたい。
子供の頃にはなかったもの
2015.10.31
カテゴリ : ローカル/占い/天気/現象
ハロウィン(Halloween)
そりゃもう街は大騒ぎさ!
トリックオアトリート!(Trick or Treat !)
ハッピーハロウィン!!(Happy Halloween!!)
ヒーユアー!(Here you are!)
せめて合言葉くらい覚えようかね
アキトの履歴書 60
2015.10.28
カテゴリ : ルーツ/アキトの履歴書
(祇園の一番花 あばれみこし 2)
伝統ある神輿も、その運行コースはあらかじめ決まっていて、
毎年、氏子から地元の宮田駐在所、駒ヶ根警察署に通行止めの許可申請をしている。
この日ばかりは、村中のみならず近隣近郊、遠方からも親戚・知人が祭り客として集まり、大変な人出となる。
村の決して広いとは言えない本通りの両側には全く空きがないほど露店が立ち並び、
その隙間を縫うように見物客が行き交う。歩くにも人、人、人で、通りはその熱気でムンムン状態となるのだ。
宮田のあばれみこしは県下に轟いていたので、その警備は厳重扱いされ、村の駐在さん一人ではとても立ち回れないと、
県警の機動隊員4人ほどが臨時に派遣されて、神輿の警備に張り付くのが“ならわし”だった。
私が、青年会の副会長そして会長だった過去2回、自宅前まで神輿を招き入れ、
皆に酒、水、御祝儀を用意し振る舞ったことは今でも自慢の種だ。当時の私に統率力がなければ不可能だっただろう。
しかし、最初に自宅前まで神輿を招いたときは、警備の警官らに
“運行のコースではない”と、即座にクレームがつけられた。
「私は役員であるし、我が家は宮田駅の目と鼻の先にあり、駅前の一部であるので文句は無かろう」
との、ずいぶん強引な話で正当化したのだが。
『火事と喧嘩は江戸の花』と云われるのと同様、
宮田の神輿(=あばれみこし)も威勢のいい時代であったかもしれない。あの頃の男子会員の中には、
“神輿は怖いから担げない”
という人が大勢居た。私は、
“万一、神輿の統率を乱す奴がいたら、つまみ出してくれ”
と仲間に頼み、実際のところ、本当にうまく進行することが出来た。
あの時の仲間・友達への感謝の気持ちは忘れない。持つべきは本物の良い仲間、友達であると痛感している。